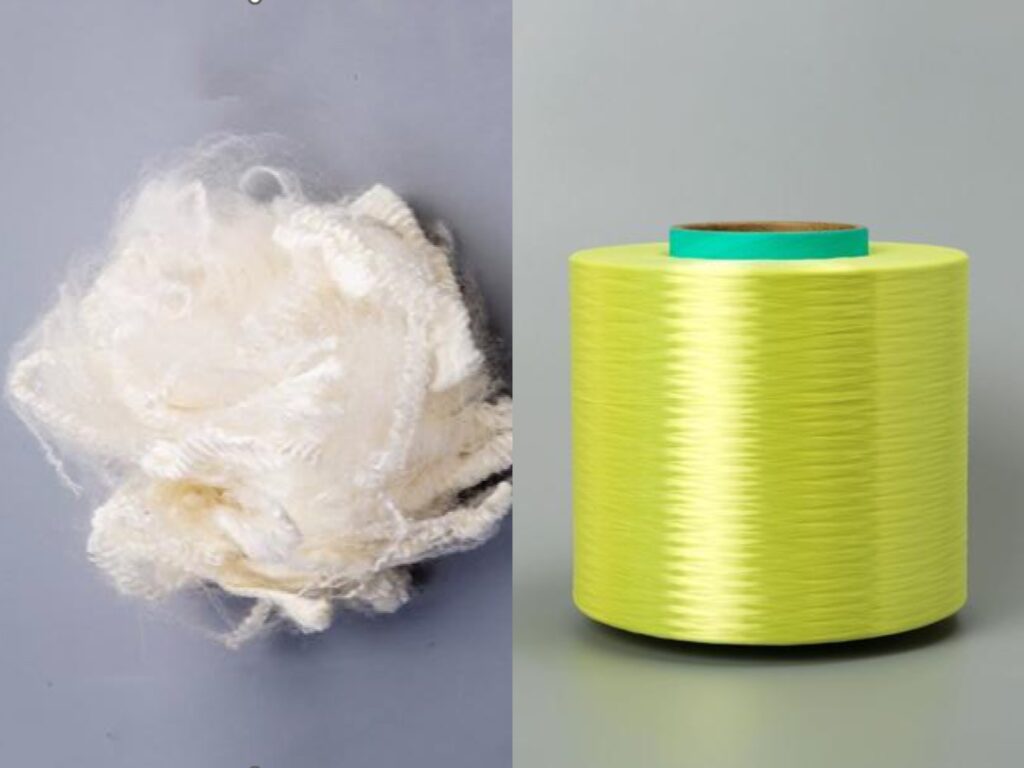
Para-aramids (e.g. Kevlar) and meso-aramids (e.g. Nomex) have significant differences in raw materials, costs and processing, which directly affect their properties and applications. The following is a systematic comparative analysis:
Differences in raw materials
Para-aramids (Kevlar class)
The main monomer:
Terephthaloyl chloride (TPC): produced by the reaction of terephthalic acid and sulfoxide chloride (SOCl₂), high purity is required to avoid side reactions.
P-phenylenediamine (PPD): strict purification is required to avoid impurities destroying the linear structure of the polymer.
Solvent: N-methylpyrrolidone (NMP) or dimethylacetamide (DMAc), high purity and high recycling rate are required.
Key property: rigid linear structure formed by linking benzene rings at 1,4 positions, depends on precise alignment of monomers.
Meta-aramid (Nomex type)
Main monomer:
Isophthaloyl chloride (IPC): simpler synthesis process (reaction between isophthalic acid and SOCl₂), slightly lower purity requirements.
Isophthalic acid (MPD): lower synthesis cost, higher impurity tolerance.
Solvent: similar to para-aramid, but with less stringent requirements for solvent recovery.
Key features: benzene ring 1,3 position connected to form a flexible chain segment, intermolecular hydrogen bonding easier to form, heat resistance enhanced.
Second, raw material cost comparison
Factors Para-aramid meta-aramid monomer synthesis difficulty is high (need high purity of para-isomer) low (meta-isomer easy to synthesize) monomer price TPC about 15-20/kg, PPD about 15-20/kg, PPD about 10-15/kg IPC about 10-12/kg, MPD about 10-12/kg, MPD about 10-12/kg, MPD about 10-12/kg. MPD about 10-12/kg, MPD about 8-10/kg Solvent cost is high (need to be recycled many times) in (recycling efficiency requirements are low) the total raw material cost accounted for para-aramid is about 60-70% for meta-aramid is about 40-50%
Description:
Para-aramid monomer synthesis requires strict control of side reactions (such as the generation of neighboring isomers), the purification process is complex; meta-aramid due to the benzene ring interstitial substitution of natural site resistance is small, the synthesis efficiency is higher.
Solvent accounts for about 20-30% of the cost, para-aramid polymerization reaction conditions are harsh (low temperature, anhydrous), solvent recovery energy consumption is higher.
Third, processing differences
- para-aramid (dry spray wet spinning process)
Polymerization:
TPC and PPD in the NMP low-temperature (0-5 ℃) polycondensation, to avoid self-crosslinking, the generation of poly(terephthaloyl-p-phenylenediamine) (PPTA).
Strict temperature and humidity control is required to prevent chain termination due to HCl by-products.
Spinning:
Dry Spray Wet Spinning: The solution is extruded from the spinneret and then passes through an air layer (stretched 5-10 times) before entering an acidic solidification bath (e.g. sulfuric acid/water) to solidify.
Process core: High-fold stretching in the air layer results in highly oriented molecular chains that form liquid crystal state structures.
Post-processing:
High-fold stretching (10 times or more): further reinforcement of molecular chain alignment.
High-temperature heat treatment (400-500℃): eliminate internal stress and enhance modulus. - Interpositional aramid (wet spinning process)
Polymerization:
IPC and MPD are polycondensed in solvent at room temperature to form poly(mesitylene mesitylene amine) (PMIA), with few side reactions.
Spinning:
Wet spinning: solution is directly extruded into the coagulation bath (e.g. CaCl₂/methanol), fibers are formed slowly, low tensile ratio (2-4 times).
High molecular chain flexibility, no need for strong stretching to form a stable structure.
Post-treatment:
Moderate stretching (3-5 times): optimization of fiber strength.
Medium temperature heat treatment (200-300 ℃): enhance heat resistance and promote the formation of hydrogen bonds. - Process Cost Comparison
Factors para-aramid meso-aramid equipment investment is very high (need precision temperature control, corrosion-resistant equipment) medium (standard wet spinning equipment) high energy consumption (low temperature polymerization + high stretch / high temperature heat treatment) low (room temperature polymerization + low stretch) process control is very difficult (need to avoid gelation, precise stretch ratio) medium (mild reaction, easy to control the parameters) the total cost of production of para-aramid ¥50-70/kg meta aramid ¥30-50/kg.