In the realm of advanced materials, carbon fiber, para-aramid fiber, and polyimide fiber each play distinct roles due to their unique properties and applications. Understanding their differences is crucial for selecting the appropriate material for specific engineering and industrial applications.
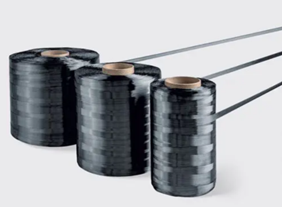
Carbon Fiber
Composition and Structure:
Carbon fiber is predominantly composed of carbon atoms, arranged in a crystalline structure parallel to the fiber’s long axis. This alignment produces a high strength-to-weight ratio, making carbon fiber exceptionally strong and lightweight.
Properties:
- High Strength and Stiffness: Carbon fiber is renowned for its high tensile strength and rigidity, often surpassing metals like steel and aluminum.
- Lightweight: With a density much lower than metals, carbon fiber significantly reduces the weight of structures.
- Thermal Conductivity: It has excellent thermal conductivity, which can benefit heat dissipation applications.
- Chemical Resistance: Carbon fiber is resistant to corrosion and chemical damage, making it suitable for harsh environments.
- Fatigue Resistance: It performs well under cyclic loads, maintaining structural integrity over time.
Applications:
Carbon fiber is widely used in aerospace, automotive, sporting goods, and civil engineering. Its high strength-to-weight ratio is ideal for aircraft components, high-performance vehicles, and lightweight sporting equipment like bicycles and tennis rackets.
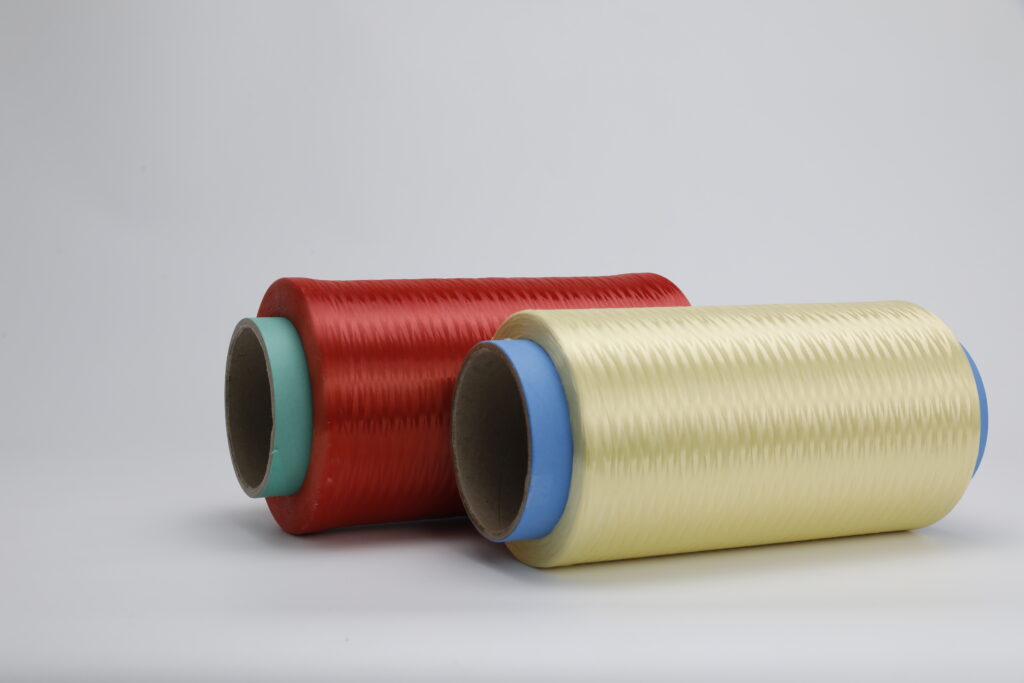
Para-Aramid Fiber
Composition and Structure:
Para-aramid fiber, known commercially as Kevlar (DuPont’s brand), is an aromatic polyamide with a highly oriented molecular structure. This orientation gives it its remarkable strength and resilience.
Properties:
- High Tensile Strength: Para-aramid fiber is extremely strong, providing substantial resistance to mechanical stress.
- Impact Resistance: It absorbs and disperses energy efficiently, making it ideal for ballistic and stab-resistant applications.
- Thermal Stability: It remains stable at high temperatures, withstanding up to 500°C without significant degradation.
- Chemical Resistance: It is resistant to most chemicals, though it can be affected by strong acids and bases.
- Low Density: Like carbon fiber, it is lightweight, contributing to its utility in protective gear and lightweight structures.
Applications:
Para-aramid fiber is commonly used in personal protective equipment, such as bulletproof vests and helmets, due to its impact resistance. It is also used in high-performance ropes, cables, and composites for aerospace and military applications.
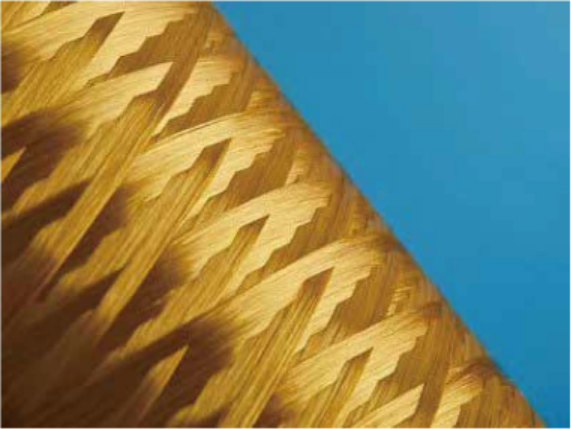
Polyimide Fiber
Composition and Structure:
Polyimide fiber is made from polyimide polymers, which contain imide monomers. The molecular structure of polyimide fibers provides high thermal stability and exceptional chemical resistance.
Properties:
- Thermal Stability: Polyimide fiber can withstand extreme temperatures, often exceeding 400°C, without losing its mechanical properties.
- Chemical Resistance: It resists a wide range of chemicals, making it suitable for use in harsh chemical environments.
- Electrical Insulation: Polyimide fiber has excellent dielectric properties, making it an effective electrical insulator.
- Mechanical Properties: It offers good tensile strength and flexibility, though not as high as carbon fiber or para-aramid fiber.
- Flame Retardancy: It is inherently flame resistant, adding to its suitability for high-temperature applications.
Applications:
Polyimide fiber is used in applications requiring high thermal resistance and chemical stability, such as in the aerospace industry for insulation and in electronics for flexible circuits and wire insulation. It is also used in filtration and protective clothing for high-temperature environments.
Comparative Analysis
Strength and Weight:
- Carbon Fiber: Offers the best strength-to-weight ratio, ideal for applications requiring both lightweight and high strength.
- Para-Aramid Fiber: Provides high tensile strength and impact resistance, suited for protective applications.
- Polyimide Fiber: While strong, it does not match the tensile strength of carbon or para-aramid fibers but excels in thermal and chemical resistance.
Thermal and Chemical Stability:
- Carbon Fiber: Good thermal conductivity and chemical resistance, but less effective in extreme chemical environments compared to polyimide.
- Para-Aramid Fiber: Excellent thermal stability and chemical resistance, though it can be degraded by strong acids and bases.
- Polyimide Fiber: Superior thermal and chemical stability, maintaining properties in extreme environments.
Specific Applications:
- Carbon Fiber: Aerospace, automotive, sports equipment.
- Para-Aramid Fiber: Personal protective equipment, high-performance ropes, military applications.
- Polyimide Fiber: Aerospace insulation, electronics, filtration, protective clothing for high temperatures.
Conclusion
Carbon fiber, para-aramid fiber, and polyimide fiber each have unique properties that make them suitable for different applications. Carbon fiber’s unparalleled strength-to-weight ratio makes it ideal for structural applications in the aerospace and automotive industries. Para-aramid fiber’s exceptional tensile strength and impact resistance make it indispensable in protective gear and military applications. Polyimide fiber’s outstanding thermal and chemical stability make it suitable for high-temperature and chemically aggressive environments. Understanding these differences ensures the right material is chosen for the right application, optimizing performance and safety.