I. Introduction Para-aramid fiber, also known as para-aramid fiber, refers to a linear polymer fiber in which the amide bond is directly connected to the benzene ring through the para position. This kind of aramid fiber was first developed and industrialized by DuPont Company. Its trade name is Kelvar, and its chemical structure is shown in Figure 1-1. The chemical structure of para-aramid fiber molecular chain has good symmetry, and its molecular chain has strong rigidity, and its solubility, rheological properties and processing methods are very different from ordinary flexible chain polymers. At the same time, in 1972, the Dutch company AKZO Nobel also developed a similar product under the trade name of Twaron, which was successfully commercialized in 1987. Figure 1-1 Chemical structure of para-aramid (Kevlar)
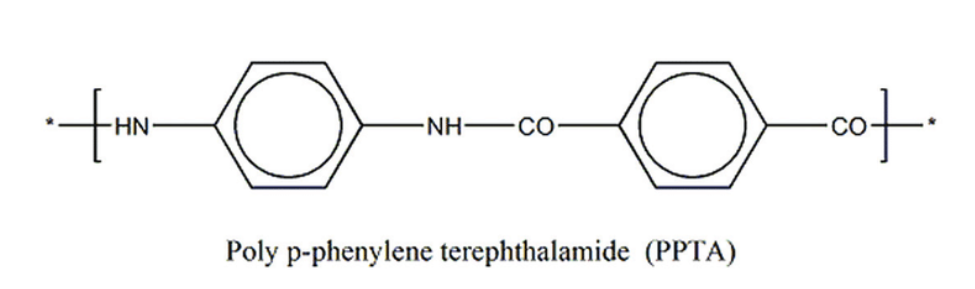
The research on para-aramid (also known as aramid Ⅱ) in my country started in 1972. At that time, the main research institutions were the Institute of Chemistry, Chinese Academy of Sciences, China Blue Chenguang Chemical Research Institute, Donghua University and so on. From 1972 to the 1990s, the development of para-aramid in my country has gone through several stages of laboratory research, small test and pilot test, and it has been listed as a national major in the “Sixth Five-Year Plan”, “Seventh Five-Year Plan” and “Eighth Five-Year Plan”. However, due to various technical problems, it has not been able to achieve industrialization [2]. Since 2000, with the promotion of market demand and the improvement of chemical technology level, many companies in my country have successively realized the industrialization of para-aramid fiber, including Zhonglan Chenguang Chemical Research Institute, Yantai Taihe New Materials Co., Ltd., SINOARA Co., Ltd. , Yizheng Chemical Fiber Co., Ltd. and other units.
After the great success of commercial application of Kevlar fiber, Teijin Corporation of Japan successfully developed terephthaloyl chloride (TPC)-p-phenylenediamine (PPD)-3,4′-diaminodiphenyl ether ( ODA) ternary copolymer fiber (trade name Technora), and realized industrial production in 1987, its chemical structure is shown in Figure 1-2. Compared with Kevlar fiber developed by DuPont, this co-aramid fiber has better flexibility and shows obvious advantages in solubility and toughness, which also provides ideas for the development of aromatic co-polyamide fiber.

Para-aramid has excellent mechanical properties, good heat resistance and corrosion resistance, which makes it widely used in the fields of composite material reinforcement, military protective material, offshore engineering and optical fiber communication. At present, the tensile strength of several kinds of para-aramid fibers that have been industrially produced abroad are all above 2.8GPa. Each fiber is divided into different grades according to the performance characteristics it focuses on. The main varieties and properties are shown in Table 1-1.
II. Synthesis of polymers and preparation of para-aramid The full chemical structure of para-aramid is polyparaphenylene terephthalamide (PPTA), which is obtained by polycondensation of terephthaloyl chloride (TPC) and paraphenylenediamine (PPD). During the polycondensation reaction, the N atom on p-phenylenediamine will attack the C atom on C and O on terephthaloyl chloride, and the elimination reaction is carried out to generate amide bond and by-product HCl. The reaction is shown in Figure 1-3. Show.
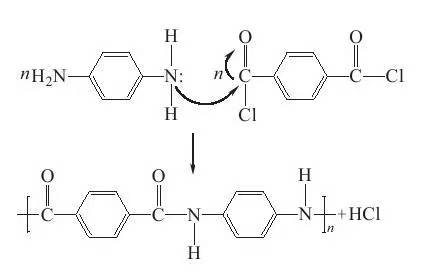
At present, the polymerization method for industrial synthesis of PPTA resin is mainly low temperature solution polycondensation. The method is to add high-purity PPD into N-methylpyrrolidone/calcium chloride (NMP/CaCl2) solvent under an inert gas atmosphere, adjust to a suitable stirring speed to completely dissolve PDA, cool down through an ice bath, add Part of TPC (melt) undergoes pre-polycondensation, and the reaction generates a pre-condensation polymer solution. Then, the pre-polycondensate solution and TPC (melt) are added to the twin-screw reactive extrusion equipment in a certain proportion through a precision metering pump, and the temperature and extrusion speed of the twin-screw are controlled. After a few minutes, a slightly lower para-benzene can be obtained. Diformic acid is synthesized, triphenyl phosphite and pyridine are added as catalysts, and a high temperature polycondensation reaction is carried out above 120°C. Some side reactions may occur during high temperature polycondensation, and high molecular weight PPTA resin cannot be obtained. Therefore, the current synthesis of PPTA resin mainly uses terephthaloyl chloride monomer with high activity [3].
Due to the high rigidity and strong inter-molecular interaction of the PPTA macro-molecular chain, the melting temperature of the PPTA resin is higher than its decomposition temperature, so that the PPTA resin cannot be melt-spun, and only solution spinning can be used. However, the PPTA macro-molecular The strong interactions between the chains make them insoluble in common organic solvents. DuPont researchers found that PPTA resin can be dissolved in concentrated sulfuric acid at 80 °C. When its concentration reaches about 10%, the solution begins to undergo liquid crystal transformation, and the apparent viscosity decreases with the increase of solution concentration [4]. When the concentration reaches 12% to 13%, the apparent viscosity reaches the lowest value, and then increases slowly with the increase of the solution concentration, but remains at a low level. When the solution concentration increased to more than 20%, the viscosity began to increase rapidly . Therefore, using the characteristics of PPTA to form liquid crystal, the PPTA resin is dissolved in concentrated sulfuric acid, compounded into a liquid crystal solution and then spun. Since the PPTA molecular chain is in a liquid crystal state, the arrangement is relatively regular, so the PPTA precursor obtained after spinning and coagulation has a high degree of orientation and crystallization, and has a high tensile strength without drafting.
The spinning of PPTA resin/sulfuric acid solution mainly adopts the dry jet-wet spinning process, which is different from the conventional wet spinning process. Dry jet-wet spinning technology was first developed by DuPont and was successfully applied to the production of PPTA fibers. Its principle can be simply summarized as the liquid crystal spinning solution is oriented in the flow direction due to the shearing action of the spinneret when the liquid crystal spinning solution is ejected from the spinneret, although a small amount of molecular chains will be generated after entering the air gap. De-orientation, but as the spinning solution gradually becomes thinner during the downward flow, the de-oriented part will be re-oriented again, so as to maintain a high degree of orientation, and then the spinning solution enters the low-temperature coagulation bath to make the orientation be reduced. Freeze, which in turn can form highly crystalline and highly oriented fibers. The modulus of para-aramid fiber will increase obviously after high temperature heat treatment, but the elongation at break and tensile strength will decrease to a certain extent. The main reason for the change in its mechanical properties is that after heat treatment, the PPTA macro-molecular chain is more tightly packed, the hydrogen bond interaction is stronger, and the crystal structure and crystal plane orientation are more perfect, which greatly increases the modulus of aramid. . The decrease in fiber tensile strength after higher temperature heat treatment may be due to the formation of pores and defects in the fiber during high temperature treatment.